Software Robots support Equipment Engineers at an oil & chemicals company
The introduction of a new software tool to develop equipment strategies had a major impact on the Engineering Division. Obviously, when adopting new technology people had to be retrained and needed get used to a new tool. The main challenge however was the impact of the new tool on the efficiency and output of the Equipment Engineers due to lack of complete data. Robotic Process Automation (RPA) has recently been introduced to help the Engineering Division eliminate this challenge.
The main challenge…..
In the transition from the old software tool to the new one, all data had to be transferred from the old database to the new database & structure. However, not all of the data was linked to the corresponding new fields available in the new tool, and some of the data was just not present in the old one. The datasets concerned are ‘Environment’, ‘Process Stream’, ‘Toxins’ and ‘Business Consequence’.
The consequence of this decision still resonates today. The Engineers need to manually retrieve data and copy it over to the relevant fields in the new tool before any actual update of an equipment strategy can take place. This manual action turns out to consume a considerable amount of valuable engineering time, impacting the overall time an engineer can focus on evergreening a strategy. A considerable <efficiency> impact to Engineers output has been observed resulting in the evergreening backlog to expand month after month since the new tool implementation. Unfortunately, in some cases, Engineers even emotionally “checked out” and indicated they wanted to stop using it.
How the company solved this challenge?
Clearly stopping use of the new software tool and reverting back to the old one was not an option. When diving deeper into the mechanisms how Engineers populate the Environment, Process Stream & Business Consequence fields in the tool it turns out this activity consist of a lot of repetitive, manual, clicking, copying, and pasting, tasks. A textbook example of low value re-occurring monotonous tasks where technology can assist and take over the tasks.
The Solution = RPA but what is RPA?
Robotic Process Automation (RPA) is a software technology that makes it easy to build, deploy, and manage software robots that emulate manual human actions, like copy-paste, interacting with digital systems and software. It performs manual tasks automatically.
One of the capable Fixed Equipment Engineers, is very proficient in the new tool and has a strong affinity with automating workflows leveraging Robotic Process Automation technology. He is the driving force behind the introduction and deployment of RPA across the Engineering Division.
The Fixed Equipment Engineer partnered with a Senior RPA Developer of Axisto Group to deliver value. He identified the workflows while the Axisto Group RPA Developer programmed them into the Robot. Within a month’s time the first workflow was up and running and only two weeks after another 2 bots were delivered and activated.
The impact of RPA = 7.5K hours saved
All Fixed Equipment is divided into so-called “parents”. For each parent identical data must be entered for each child component. The site has a total of 5,839 parents containing a total of 34,834 components. Automatically pre-populating all components for Environment, Process Flow and Business Consequence by leveraging RPA saves the Engineers in total about 7,500 hours or about 5.5 man-years. Next to reducing impact on ergonomics by eliminating and automating tedious clicking/copy-paste activities we see more potential savings linked to RPA in the context of equipment strategies as site wide, including non-fixed, we have about 11,703 parents for all equipment…..
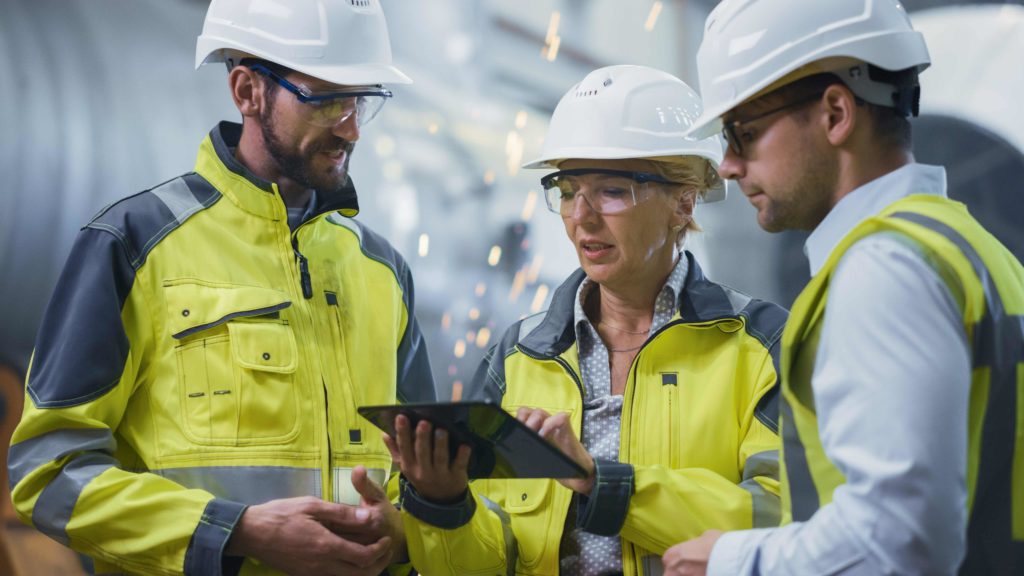